
وارنیش شدن روانکارها و راه های کاهش آن
LUBE-OIL MAINTENANCE:Lubricant varnishing and mitigation strategies
By Peter Dufresne Jr, Matthew G Hobbs, Glen MacInnis, EPT
COMBINED CYCLE JOURNAL, Fourth quarter 2013
در حدود ۱۰ سال پیش، شرکت جنرال الکتریک، مشاهده علایم وارنیشی شدن روغن در تقریباً یک از سه توربین بزرگ گاز صنعتی را گزارش داد. از آن جایی که این شرایط بر قابلیت اطمینان و دسترسی توربین های گازی تاثیر دارد، بنابراین سازندگان تجهیزات استفاده از سیستم های حذف وارنیش را پیشنهاد دادند. با وجود این توصیه وارنیش خروجی توربین ها، موضوع قابل توجهی در صنعت باقی ماند.
اولین دلیلی که وارنیش یک مشکل مداوم به شمار می آید این است که : صاحبان صنایع ، از مکانیسم تشکیل وارنیش درک ضعیفی دارند. به همین دلیل راهکارهایی که جهت خذف و اصلاح مشکلات وارنیش طراحی می شود به هدف نهایی نمی رسند و نتایج آن کمتر از حد انتظار است. این مقاله (ارائه شده توسط نویسنده اصلی در کنفرانس Frame 6Users Group 2013) قصد دارد با بحث پیرامون دلایل ویژه تشکیل وارنیش و گزینه های متنوع به منظور کاهش تاثیرات عملکردی آن، درک ما از وارنیش را بهبود ببخشد.
تشکیل وارنیش
به طور کلی، به رسوب نازک، سخت، براق و نامحلول روغن که در مرحله اول از پس ماندهای آلی تشکیل می شود، وارنیش گفته می شود(شکل ۱). میزان وارنیش معمولاً توسط شدت و رنگ آن مشخص شده و به راحتی از اجزای سیستم زدوده نمی شود.
این تعریف از وارنیش، تنها به توصیف بخش انتهایی چرخه عمر آن اختصاص دارد. توصیف مناسبی که تمام چرخه وارنیش را در بَربگیرد، به صورت زیر بسط داده می شود: وارنیش، با تشکیل محصولات محلول ناشی از کاهش کیفیت، عمر خود را آغاز می کند. فرآیند مربوط به رسوب دهی وارنیش به صورت ذرات برگشت پذیر است.
این تعریف بسط یافته جابه جا پذیری در شکل ظاهری وارنیش را آشکار می کند. وارنیش می تواند نامحلول بوده (همان طور که به طور مرسوم از شکل ذره ای آن تشخیص داده می شده) یا آن که در سیال حل شده باشد. (محلول). آگاهی از میزان حلالیت روانکار، کلید فهم مکانیسم تشکیل رسوبات وارنیشی و مهم تر از آن مکانیسم حذف آن است.
حلالیت روانکار
در شرایط عادی عملکرد روانکارهای توربین ها، در معرض اکسایش و به دنبال آن تولید مولکول های قطبی (پیش سازهای وارنیش[۱]) از نوع غیر قطبی آن (استوک های روغن پایه معدنی روانکارها) است . این گونه های قطبی، آغازگر چرخه عمر وارنیش هستند. در نتیجه، روانکار در حالِ کار به ترکیب پیچیده ای از استوک های پایه، افزودنی ها و آلودگی تبدیل می شود.
از ناتوانایی روانکار در حل کردن این اجزای مشخص، به «حلالیت روانکار[۲]» تعبیر می شود. همه اجزای روغن انحلال پذیری محدودی داشته که از عوامل متعددی تاثیر می پذیرند (مانند قطبیت مولکولی، سطح آلودگی، دما و …). این انحلال پذیری است که تعیین می کند یک مولکول خاص، محلول در سیال باشد یا از آن به صورت رسوب جدا شده و ذراتی با پتانسیل تخریب بیشتر را ایجاد نماید.
زمانی که انحلال پذیری مولکول کم باشد، روانکار نمی تواند آن را حل کند و به طور فعال آن را به صورت رسوب از خود جدا می کند. در حالی که وقتی انحلال پذیری مولکول زیاد باشد، ظرفیت روانکار برای حل آن افزایش یافته و از تشکیل رسوبات وارنیشی جلوگیری می شود.
عوامل موثر بر حلالیت روانکار
عوامل زیر نقش مهمی را در فرآیند انحلال پذیری پیش سازهای وارنیش در روانکار بازی می کنند.
قطبیت مولکولی. قطبیت مولکول ها به توزیع بارهای مثبت و منفی در مولکول برمی گردد. در برخی مولکول ها، این بارها به خوبی از هم جدا شده اند (درست مثل قطب های آهن ربای میله ای). به چنین مولکول هایی قطبی گفته می شوند. در مابقی مولکول ها، جدا شدن بارها ناچیز بوده یا وجود ندارد. در این صورت، به این مولکول ها غیر قطبی گفته می شوند.
تفکیک قطبیت یا غیر قطبی بودن مولکول ها به سادگی سیاه و سفید نبوده و طیفی از خاکستری را شامل می شود. از آن جایی که قطبیت به ساختار ویژه هر مولکول بستگی دارد، یک مولکول خاص می تواند قطبیت کمتر یا بیشتری از مولکول دیگر داشته باشد.
قاعده کلی این است که «مشابه، مشابه را حل می کند». طبق همین قاعده است که الکل قطبی در آبِ به شدت قطبی حل می شود، در حالی که آب قطبی در روغن معدنی غیر قطبی نامحلول است. پیش سازهای وارنیش که محصول کاهش کیفیت و در نتیجه اکسایش استوک های پایه روغن معدنی هستند، قطبیت خیلی کمتری نسبت به آب دارند، لکن این محصولات با کاهش کیفیتِ تا حدی قطبی در بستر غیرقطبی روغنِ معدنی انحلال پذیری محدودی دارند. هرچه محصولات کاهش کیفیت و قطبیت بیشتری داشته باشد، حلالیتشان کم تر است.
سطوح آلودگی روانکار. روانکار، ظرفیت محدودی جهت حل کردن سایر مولکول ها دارد (مانند افزودنی ها، آلودگی ها، پیش سازهای وارنیش و …). همان طور که به مرور روغن کاهش کیفیت داده و محصولات حاصل از اکسایش آن انباشته می شوند، حلالیت سیال نیز به همان نسبت کاهش می یابد. مدتی نمی گذرد که سیال نمی تواند پیش سازهای وارنیش تشکیل شده از اکسایش مستمر روغن را در خود جای دهد و در نتیجه وارنیش به صورت جامد از آن جدا شده و رسوب می کند.
دما. دمای روغن به طور مستقیم بر انحلال پذیری تمام گونه های محلول در آن اثر می گذارد. همان طور که دما کاهش می یابد، انحلال پذیری وارنیش و پیش سازهای آن نیز کاهش می یابد. در صنعت قند و شکر، قالب های حاوی محلول شکر داغ، جهت کاهش انحلال پذیری شکر سرد می شوند به دنبال کاهش حلالیت شکر بلورهای خطی شکر از محلول جدا می شوند. فرآیند مشابهی در مناطق خنک سیستم گردش روانکار توربین منجر به رسوب دهی ذرات وارنیش می شود. از آن جایی که فلزات از استوک پایه روانکار قطبی تر هستند، رسوبات قطبی وارنیش ترجیح می دهند به فلزات بچسبند و رسوبات با توانمندی آسیب زننده را تشکیل دهند. زمانی که سطح پیش سازهای وارنیش در روانکار به نقطه اشباع سیال (یا نزدیک آن) می رسد، وارنیشی شدن در مناطق خنک بسیار محتمل است.
چرخه وارنیش
چرخه معمول تشکیل وارنیش در توربین گازی شامل سه مرحله است(شکل ۲).
. اکسایش یک واکنش شیمیایی بین روغن پایه روانکار و اکسیژن موجود در هوای اطراف آن است. اکسایش یک فرآیند اجتناب ناپذیر بوده و به محض آن که سیال جدید برای اولین بار در معرض هوا قرار می گیرد بدون توجه به این که آیا سیال در حال کار هست یا نه، آغاز می گردد. مشابه تمام واکنش های شیمیایی دیگر، سرعت اکسایش از معادله آرنیوس تبعیت می کند. مطابق این معادله با افزایش هر ۱۰ درجه سانتی گراد یا ۱۸ درجه فارنهایت، سرعت واکنش دو برابر می شود.
زمانی که سیال جدید شروع به کار می کند، در معرض دمای بالاتری قرار می گیرد و در نتیجه سرعت اکسایش در آن افزایش می یابد. حتی زمانی که دمای عملکرد به دمای نوعی °F 125 (°C7/51) می رسد، دمای یاتاقان ها ممکن است به بیش از °F 300 (°C9/148) برسد. در این مثال سرعت اکسایش در یاتاقان بیش از ۱۰۰ برابر بیشتر از مناطق خنک تر سیستم می شود. در نتیجه، معمولاً اکسایش زمانی قابل توجه است که نقاط داغ ایجاد می شوند. همواره محصولات حاصل از اکسایش در حال ساخته شدن در روانکار هستند، لکن در دمای عملکرد به صورت محلول هستند مگر آن که به نقطه اشباع در سیال برسند.
. در حالی که روغن از مناطق داغ تر سیستم به مکان خنک تر حرکت می کند (برای مثال، خطوط هیدرولیکی که روغن با فشار بالا را به سمت بخش کنترل موتور هدایت می کند)، دمای سیال افت کرده و انحلال پذیری پیش سازهای وارنیش موجود، کاهش می یابد. این پیش سازها شروع به رسوب دهی از محلول کرده و به صورت ذرات نشست می کنند. مشابه انجماد آب و تشکیل یخ، تشکیل این رسوبات وارنیشی نیز یک تغییر فیزیکی به شمار آمده و واکنش شیمیایی نیست.
. زمانی که ذرات وارنیش متراکم شده و رسوبات تشکیل می شوند، ترجیح می دهند سطوح فلزی را بپوشانند. این رسوبات اغلب لغزش دستگاه یا خطا در شروع را موجب می شوند. مشابه رسوب دهی در مرحله ۲ (در شکل بالا)، تراکم و انباشتگی ذرات نیز تغییر فیزیکی به حساب می آید.
این مدل از تشکیل وارنیش به طور وسیعی پذیرفته و به خوبی فهمیده شده است. آنچه که به خوبی درک نشده، این واقعیت است که زمانی که رسوبات وارنیش شکل می گیرند اگر حلالیت روانکار افزایش یابد می توانند باز جذب شوند. در حالی که تغییرات شیمیایی سبب ایجاد پیش سازهای وارنیشِ برگشت ناپذیرند (قدم ۱)، تغییرات فیزیکی که تشکیل رسوبات وارنیشی را موجب می شوند برگشت پذیرند (قدم ۲ و ۳). راهبردهای موفق در کاهش وارنیش از چنین واقعیتی بهره می برند.
آزمودن وارنیش
در نتیجه امکان وقوع خرابی های پر هزینه توربین ناشی از وارنیشی شدن، ضروری است تمایل روانکار به تشکیل رسوبات وارنیشی تعیین شود. بیشتر استفاده کنندگان توربین، جهت بررسی امکان حضور وارنیش در روانکارها به طور وسیعی از تکنیک های پذیرفته شده نظیر QSA (آنالیز طیف سنجی نوری کمی) و آزمون استاندارد MPC (رنگ سنجی تکه غشایی ASTM7843) استفاده می کنند. روش های اختصاصی آزمون وارنیش (روش های غیراستاندارد)، توصیه نمی شوند، چرا که این آزمون ها به طور وسیع استفاده نشده و نمی تواند مورد تایید باشد. آنالیزهای دیگر تاکید شده، مانند اندازه گیری وزن پچ می تواند به سلامت روغن کمک کند.
نتایج هر دو روش اندازه گیری وارنیش در بالا، به طور قابل توجهی به طول عمر نمونه روغن بستگی دارد. در واقع نمونه با طول عمر بیشتر مقادیر MPC بالاتری را تولید می کند که نشان دهنده کاهش کیفیت مستمر روانکار در نمونه بطری است. به همین دلیل روش ASTM در آزمون MPC پیشنهاد می دهد که تمام نمونه ها پس از قرارگیری در دمای°F 140 به مدت ۲۴ ساعت، به مدت ۷۲ ساعت نیز در دمای اتاق نگه داشته شوند. این نوع زمان دهی استاندارد شده و به خوبی تشریح شده موجب ثبات شرایط درون آزمایشگاهی و بهبود تکرار پذیری می شود.
افزایش مقادیر MPC و QSA در مدت نگهداری نمونه، در نتیجه گسترش روند واکنش های اکسایشی است که در واقع، زمانی که روانکار در حال کار بوده آغاز شده است. روغن هایی که روند کاهش کیفیت را در بطری نمونه نیز ادامه می دهند درمخزن روانکار نیز می توانند کاهش کیفیت می دهند. این مساله، ضرورت استفاده مستمر از دستگاه حذف وارنیش را خاطر نشان می کند. درعدم حضور چنین دستگاهی، روغن مخازن با تجمع محصولات حاصل از تخریب مواجه شده و حتی در زمانی که توربین کار نمی کند تشکیل وارنیش را ادامه دهند.
راهبردهایی برای مبارزه با وارنیشی شدن
بیشتر روانکارهای توربین های مدرن از استوک های پایه روغن معدنی گروه ۲ API که همراه با بسته افزودنی آنتی اکسیدانی، ساخته شده است. ساختار شیمیایی استوک های پایه گروه ۲ که افزایش پایداری روانکار در مقابل اکسایش نسبت به استوک های پایه گروه ۱ را موجب می شود سبب جایگزین شدن آن ها در کاربردهای روغن توربین شده است(شکل ۳).
آنتی اکسیدان ها معمولاً به عنوان راهبردی جهت کاهش وارنیشی شدن به روانکار افزوده می شوند. این افزودنی ها خود شامل دو دسته شیمیایی اند : فنول ها و آمین ها. هر چند، هرکدام از این ها به تنهایی خواص آنتی اکسیدانی دارند لکن در صورت هماهنگی با یکدیگر بسیار کاراتر عمل می کنند. زمانی که مقدار و نوع مشخصی از آنتی اکسیدان ها در روانکارهایی با فرمولاسیون متفاوت به کار گرفته می شود مکانیسم افزایش طول عمر سیال یکسان باقی می ماند.
این افزودنی های شیمیایی راحت تر از استوک پایه روغن روانکار اکسید می شوند. در نتیجه سرعت اکسایش خودِ روغن تا زمانی که آنتی اکسیدان ها حضور دارند، کاهش می یابد. متاسفانه هر دوی آمین ها و فنول ها به دنبال اکسید شدن، مصرف می شوند. فنول ها، سریعتر خالی می شوند. زمانی که افزودنی ها مصرف می شوند سرعت کاهش کیفیت سیال افزایش یافته، دوباره مشابه استوک پایه بدون افزودنی می شود (شکل ۳). آنتی اکسیدان ها سرعت کاهش کیفیت در نتیجه اکسایش را محدود کرده و بنابراین وارنیشی شدن را به تاخیر می اندازند، لکن نمی توانند از آن جلوگیری کنند.
از آن جایی که سطح آنتی اکسیدان ها به طور مستمر کاهش می یابد، پایش آن ها به منظور اطمینان از میزان کاهش کیفیت روانکار ضرورت دارد. روش هایی برابر پایش خالی شدن از افزودنی ها وجود دارد، نظیر ولتامتری[۱] (آزمون RULER, ASTM6971)، طیف سنجی تبدیل فوریه مادون قرمز[۲] (FTIR) و کروماتوگرافی مایع با فشار بالا[۳] (HPLC). صرف نظر از روشی که به کارگرفته می شود، زمانی که افزودنی های آنتی اکسیدانی به طور کامل مصرف می شوند سیال باید جایگزین شود.
در حالی که افزودنی های آنتی اکسیدانی در اغلب فرمولاسیون های روغن توربین، ابزار ضروری جهت مبارزه با وارنیش هستند، همان طور که ذکر شد تنها می توانند کاهش کیفیت در نتیجه اکسایش را محدود کرده و توانایی جلوگیری از بروز آن را ندارند. زمانی که روانکار به ناچار اکسید شده و پیش سازهای وارنیش تشکیل می شود به کارگیری سیستم های حذف وارنیش جهت جلوگیری از تجمع محصولات کاهش کیفیت و به دنبال آن وارنیشی شدن ضرورت دارد. دو نوع سیستم حذف وارنیش وجود دارد: یکی براساس حذف ذرات معلق (نامحلول) است و دیگری براساس حذف ذرات محلول و پیش سازهای آن.
[۱] Voltammetry
[۲] Fourier Transform InfraRed Spectroscopy
[۳] High-Pressure Liquid Cromatography
سیستم حذف ذرات معلق. فیلتراسیون عمیق، تجمع بار موازنه شده، زدودن روغن توسط الکتریسیته ساکن و یا ترکیبی از این تکنیک ها گونه های پیشرفته ای از حذف ذرات هستند. این تکنیک ها ذرات ریزی که در سیال معلق هستند، از جمله ذرات نامحلول وارنیش را حذف می نمایند. مشابه سایر فناوری های حذف ذرات، این سیستم ها باید قبل از ان که مقدارشان قابل توجه شود باید منتظر تشکیل ذرات نامحلول باشند.
از آن جایی که حلالیت در دمای پایین تر کاهش می یابد(در راستای خواسته مطلوب تشکیل ذرات نامحلول)، بیش ترین کارایی این سیستم ها زمانی حاصل می شود که توربین در حال کار نبوده و روانکار در دمای محیط باشد. بنابراین سیستم های حذف ذرات معلق، اغلب به صورت دوره ای در مدتی که دستگاه خاموش است به کارگرفته می شوند. استفاده از این سیستم ها به طور مستمر و در زمان کار کردن توربین کارایی چندانی ندارد. با در نظر گرفتن شرایط مذکور، این سیستم ها قادر به حذف وارنیش محلول و پیش سازهای آن نیستند.
در تلاش برای غلبه بر چنین محدودیتی و امکان استفاده مستمر از آن، خنک کننده های روغن در ورودی این سیستم ها می توانند به کار گرفته شوند تا بلافاصله قبل از عبور از سیستم های حذف وارنیش با ایجاد شتاب در چرخه تشکیل وارنیش، رسوب دهی ذرات نامحلول از روانکار را موجب شوند. چنین شکلی از حذف وارنیش تحت عنوان «حذف وارنیش توسط دمای القا شده » شناخته می شود.
هرچند در حجمی از روغن که می تواند خنک شود، محدودیت وجود دارد: روغن سرد، گرانروی بیشتری داشته و به سختی از سیستم حذف ذرات عبور می کند. به دلیل این محدودیت، روغن نمی تواند تا دمای مورد نیاز جهت حذف کامل همه وارنیش محلول موجود خنک شود. نتیجه: انحلال پذیری روانکار نمی تواند به نقطه ای برسد که تمام رسوبات وارنیشی حاضر در جای دیگر سیستم بتوانند دوباره جذب سیال شوند.
علاوه بر این، وارنیش محلول و پیش سازهای آن که نمی توانند از سیال جدا شوند به توربین برگردانده شده و روی سطوح فلزی می نشینند. همان طور که وارنیش رسوب می کند، روانکار نیز به تدریج اشباع شده و در حذف وارنیش اختلال بیشتری ایجاد می شود. به دنبال تشکیل مستمر وارنیش، اغلب سیستم حذف ذرات معلق نمی تواند به کار خود ادامه دهد.
سیستم های حذف وارنیش محلول (SVR) از پیوند بار – یون تخصصی شده (ICB) در زرین های تبادل یونی استفاده می کنند. این زرین ها در بردارنده میلیون ها جایگاه قطبی دارای قابلیت جذب سطحی وارنیش محلول و پیش سازهای آن هستند. این جذب سطحی در نتیجه برهم کنش مولکولی گزینش پذیر مابین مولکول های وارنیش قطبی و جایگاه های قطبی حاضر در طول زرین حاصل می شود. بیش از آن که وارنیش قطبی به پوشاندن سطوح فلزی تمایل داشته باشد به جذب سطحی روی جایگاه های قطبی زرین ICB علاقمند است.
زرین های تبادل یونی مرسوم، از طریق تعویض یک گونه شیمیایی با نوعی دیگر عمل می کنند. بر خلاف این زرین ها که یک آلودگی را با گونه دیگری تعویض می کند، زرین های ICB به گونه ای طراحی شده اند که تمام آلودگی ها را بدون برگشت گونه ای دیگر به سیال جذب سطحی می کنند.
مزیت کلیدی جذب سطحی ICB این است که محصولات اکسایش مضر می توانند به طور مستمر و در هر دمایی، توسط سیستم SVR حذف شوند. حذف مستمر وارنیش محلول و پیش سازهای آن این اطمینان را می دهد که محصولات کاهش کیفیت در روانکار انباشته نشده و خطر تشکیل وارنیش حین خاموش شدنِ معمول توربین ها حذف می شود. علاوه بر این حذف مستمر وارنیش محلول، حلالیت بی اندازه بالای روانکار را موجب می شود.
از آن جایی که تشکیل ذرات نامحلول تغییر فیزیکی بوده و رسوب دهی برگشت پذیر است، در نتیجه حلالیت بالای روانکارهای عمل آوری شده با SVR، وارنیش نامحلول موجود بر سطوح توربین به وارنیش محلول تبدیل شده و به سیال بر می گردند. در این صورت می توانند جذب سطحی شده و حذف گردند. با حذف کامل محصولات جانبی حاصل از اکسایش پسماند، چرخه تشکیل وارنیش به طور کامل متوقف می شود.
شکل ۴ تغییرات مقدار MPC در طول یک سال بعد از نصب سیستم SVR را نشان می دهد. دو فاز مشخص در این مثال وجود دارد. اولین فاز مربوط به «ترمیم » یا «تمیز شدن » است. دومین فاز «فاز پایدار » را نشان می دهد. زمانی که عمل آوری SVR آغاز شده و فاز ترمیم شروع می شود، مقدار MPC ابتدا زیاد می شود. برای بسیاری از کاربران، افزایش ابتدایی در ا مکان حضور وارنیش پس از نصب SVR، نگران کننده است. هرچند چنین افزایشی معمول بوده و نشان می دهد سیستم SVR به هدف خود رسیده است.
در این وضعیت، جهت زدودن رسوبات وارنیش نامحلول مذکور و برگرداندن آن ها به حالت محلول، افزایش حلالیت روانکار مورد نظر است. بنابراین سطح وارنیش محلول در اندازه گیری MPC افزایش می یابد. فاز ترمیم،به مدت سه تا چهار ماه یا حتی بیشتر، بسته به میزان آلودگی موجود به طول می انجامد.
زمانی که سیستم نسبتاً تمیز شد و تنها مقدار ناچیزی از رسوبات وارنیش باقی ماند (ویا فاقد رسوبات وارنیش شد)، امکان حضور وارنیش در سیال با استفاده از SVR، افت ناگهانی می کند. زمانی که مقدار MPC به زیر ۱۰ می رسد، وارد فاز پایدار می شود. در این حالت، روغن حاوی حداقل سطح از محصولات حاصل از اکسایش پیش سازهای وارنیش بوده و حلالیت بالایی دارد. عملکرد توربین تحت این شرایط به بهترین حالت می رسد. با افزایش حلالیت روانکار و پایین بودن غلظت پیش سازهای وارنیش محلول، از تشکیل وارنیش در دماهای متفاوت عملکرد و شرایط تحت فشار به کار گرفته شده درتوربین ها، جلوگیری می شود.
حذف وارنیش محلول
ذرات وارنیش و رسوبات مربوطه از تغییرات فیزیکی برگشت پذیر ساخته می شوند. تغییراتی که در حضور محصولات محلول حاصل از اکسایش شروع شده و به تشکیل رسوبات نامحلول ختم می شود. برای برگشت پذیر بودن این تغییرات لازم است خواص شیمیایی رسوبات و روانکاری که رسوبات از آن ساخته شده، مشابه باشد. معمولاً زمانی که حلالیت سیال افزایش می یابد (در نتیجه حذف وارنیش محلول در دمای معمول عملکرد) رسوبات به راحتی به صورت محلول وارد سیال شده و حذف می شوند.
(شکل ۴) اگر چه زمانی که یک روانکار با روانکار دیگر جایگزین می شود، ممکن است قابلیت برگشت رسوبات یا ذرات وارنیش باقیمانده به حالت محلول از دست برود. بنابراین تغییر فوری روغن موجب باقی ماندن مقدار قابل توجهی از وارنیش روی سطوح توربین می شود. به همین دلیل مخزن های قدیمی باید قبل از تعویض روغن تمیز شوند. فرآیند ICB می تواند با بازگرداندن حلالیت سیال، به رسوبات ساخته شده توسط روانکار اجازه دهد تا به صورت محلول در آمده و حذف شوند. در این صورت مخزن تمیز شده و بدون آن که پسماندی داشته باشد، آماده تعویض روغن است.
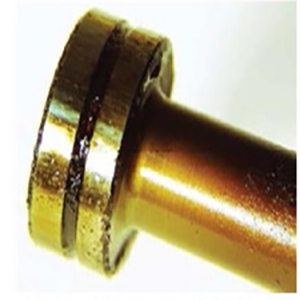
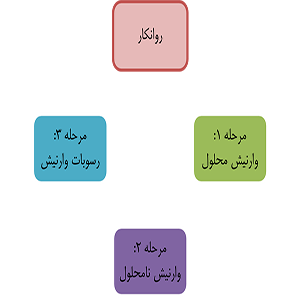

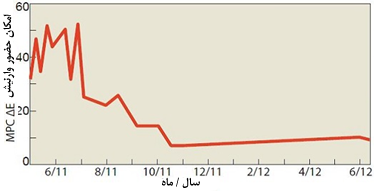