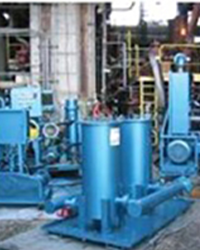
CostEffective Alternatives for Flushing Turbine Oil Systems
A Noria publication: Machinery Lubrication
انتخاب های موثر و به صرفه جهت فلاش کردن سیستم های روغن توربین
اش کردن روغن[۱] یک اصطلاح کلی است که به منظور توصیف فعالیت های متنوع جهت حذف آلودگی های سیستم روانکار و تمیز کردن قطعات درونی سیستم شما استفاده می شود. ASTM D6939، فلاش کردن را این گونه تعریف می کند: «گردش سیال از میان سیستم روانکار و یا قطعه به منظور حذف آلودگی ها، در زمانی که توربین کار نمی کند.»
راه های بسیاری برای بازگرداندن تمیزی سیستم روانکار وجود دارد. جهت انتخاب روش مناسب فلاش کردن روغن، باید مواردی از قبیل اهداف کلی دستگاه، نوع آلودگی های سیستم و وضعیت قطعات سیستم روانکار، مورد توجه قرار گیرد.
[۱] oil flushing
فلاش کردن یا نکردن
فلاش کردن، در صورت نیاز و انجام موثر، یک روش نگهداری با ارزش برای دستگاه هاست. بازگرداندن تمیزی سیستم، می تواند عمر تجهیزات شما را افزایش دهد. هر چند فلاش کردن روغن برای هر سیستم روانکاری، یک عمل تخریبی بوده و در صورت عدم اجرای مناسب، خطر قابل توجهی را به همراه دارد. اولین قدم ، تشخیص نیاز سیستم شما به فلاش کردن است.
نیاز به فلاش کردن روغن در موقعیت های زیادی، پیش می آید: مانند راه اندازی دستگاه های جدید و یا دوباره راه انداختن دستگاه هایی که مدت طولانی کار نکرده اند، بعد از بروز اشکال در سیستم قطعات و رها شدن تکه های شکسته شده در سیستم روانکار، بعد از ناکارآمد شدن فیلتر و برگشت آلودگی ها به سیستم، زمانی که یک سیال غیرسازگار ناخواسته به سیستم اضافه می شود، زمان تعویض روغن با یک برند و یا فرمولاسیون جدید روانکار و عدم درک ناسازگاری آن، و یا زمانی که محصولات ناشی از کاهش کیفیت روغن مانند لجن و وارنیش در سیستم حضور دارند.
در بیشتر مواقع، کاربران روغن توربین، مابین تعویض روغن، بدون آن که اشکال فاجعه سازی اتفاق افتاده باشد، اقدام به فلاش کردن روغن می کنند. اما آیا در هربار تعویض روغن، فلاش کردن آن لازم است؟ یک روش پذیرفته شده همگانی صنعتی برای تعیین آن وجود ندارد. حذف روغن کاهش کیفیت داده و رسوبات از قطعات داخلی سیستم روانکار شما، قبل از تعویض روغن با روغن نو، مطمئناً، منطقی به نظر می آید. کسی دوست ندارد در یک وان کثیف، حمام کند! با وجود هزینه بر بودن فلاش کردن روغن، آیا واقعاً ضروری است؟
در صورتی که سیستم روانکار عاری از لجن، وارنیش و سایر رسوبات باشد، امکان حذف بیشتر روغن مصرف شده از سیستم وجود داشته باشد، روغن توربین جدید از یک نوع و برند روغن در حال کار باشد و یا آزمون سازگار بودن روغن را بررسی کرده باشند، فلاش کردن، ضرورتی ندارد.
به عبارت دیگر فلاش کردن روغن باید زمانی اجرا شود که نشانی از حضور لجن، وارنیش و سایر رسوبات در سیستم وجود داشته، روغن در حال کار فعلی در وضعیت نامناسب شیمیایی یا فیزیکی بوده و امکان عملی حذف بیش از ۹۸ درصد روغن از سیستم وجود نداشته باشد. روغنی که می خواهد اضافه شود، فرمولاسیون متفاوت داشته به طوری که با روانکار فعلی سازگار نباشد.
تاثیر ریختن روغن توربین نو در سیستم آلوده
از آن جایی که اولین وجه از بروز اشکال در روغن توربین، اکسیداسیون آن است، عمر و بازدهی روغن توربین به سلامت بودن سیستم ضداکسیدانی بستگی دارد. دوباره افزودن روغن نو به روانکار کثیف، می تواند بر عمر و بازدهی روغن جدید، اثر بگذارد. محصولات کاهش کیفیت روغن، گونه های فعالی هستند که خیلی سریع سیستم را از آنتی اکسیدان های تازه، عاری می کنند. سایر خواص مانند اسیدیته، قابلیت جداپذیری آب، بازدارندگی از کف، همگی می توانند تحت تاثیر باقیمانده های وارنیشی و لجن موجود در سیستم قرار گیرند. مثال های زیر، نشان می دهند که چرا افزودن روغن نو به سیستم آلوده می تواند اثرات مضری داشته باشد.
مخزن[۱] سیال هیدرولیکی کشتی
کشتی های بزرگ، اغلب از روغن های بازدارنده اکسیداسیون و ضد زنگ، به عنوان سیال هیدرولیکی، جهت کنترل سیستم های پروانه با گام متغیر[۲] استفاده می کنند. کشتی که در شکل ۴ توصیف شده سالانه تعمیرات اساسی شده و سیال هیدرولیکی آن در زمانی که عدد اسیدی آن بالاتر از ۲/۰ میلی گرم پتاسیم هیدروکسید در گرم (mg KOH/g) را نشان دهد، تعویض می شود. کشتی، مابین تعویض روغن ها، فلاش نمی شود. شکل ۴، نتیجه چنین شیوه نگهداری برعمر روغن را نشان می دهد.
[۱] sump
[۲] controllablepitch propeller
توجه کنید که عمر مفید سیال بعد از هر سه تعویض روغن، از ۵ سال در اولین تعویض به ۳ سال بعد از دومین تعویض و یک سال بعد از سومین تعویض کاهش می یابد. همچنین بعد از هر چرخه تعویض روغن، ارزش سیال به میزان قابل توجهی از دست می رود. با وجودی که سیال مشابه استفاده شده و عملکرد سیستم نیز مشابه بوده است، تعویض های روغن، در افزایش عمر مفید آن کمتر تاثیر داشته است.
زمانی که کشتی به عمر ۹ ساله خود رسید و بعد از تنها یک سال، سومین تعویض روغن نیاز شد، فلاش کردن سیستم اجرا شد، این عمل موجب شد تا همه محصولات کاهش کیفیت سیستم حذف شوند. این فلاش کردن روغن، تمیزی سیستم را برگرداند و تعویض مجدد روغن را یک بار دیگر به پنج سال بعد موکول کرد.
مخزن توربین گازی فریم بزرگ
وقتی که روغن در توربین گازی فریم بزرگ، تعویض شد، فلاش کردن آن انجام نشد. روغن مصرفی کاهش کیفیت داد و در کار شیرهای دستگاه، به علت حضور وارنیش در سیستم اِشکال پیش آمد، تاثیر تمیز نکردن ناکافی سیستم قبل از اضافه کردن روغن نو، در جدول ۱ نشان داده شده است.
همان گونه که در جدول ۱، نشان داده شده است، بعد از یک هفته استفاده، میزان آنتی اکسیدان ۲۶ درصد کاهش یافته است. این مساله به دلیل واکنش بین آنتی اکسیدان ها و آلودگی های به جا مانده در سیستم است. همچنین در این کاربرد، امکان حضور وارنیش، خارج شدن از طبقه بندی نرمال را تشدید می کند. در این مورد، تمیز نکردن سیستم قبل از پرکردن با روغن نو، عمر روغن را تقریباً ۳۰ درصد کاهش می دهد. همچنین کارایی روغن نیز کاهش می یابد، که بر قابلیت اطمینان و دسترسی دستگاه تاثیر گذار خواهد بود.
درکی از واکنش پذیری تکه های وارنیش
یک آزمایش ساده، جهت درک واکنش پذیری خود وارنیش و تاثیر آن بر روغن نو، انجام شد. فیلتری که حاوی رسوبات وارنیشی قابل توجه بود، ابتدا توسط اتر نفتی شستشو یافت تا روغن آن زدوده شود و وارنیش روی واسطه باقی بماند. وارنیش برجای مانده بر واسطه، در بِشِری از روغن نو قرارداده شده و به مدت یک روز با آن هم زده شد. آنالیز با تبدیل فوریه مادون قرمز (FTIR) بر روی روغن، بعد از ۴۸ ساعت انجام شد. رنگ روغن به میزان قابل توجهی تغییر یافت و برخی از تکه های وارنیش روی فیلتر، حل شد. همچنین افزوده شدن محصولات ناشی از کاهش کیفیت در روغن توسط طیف FTIR تایید شد.
طبق نتایج آنالیز، مشخص شد که غلظت قابل توجهی از آنتی اکسیدان های آمینی از سیال نو، ناپدید شده اند. این آزمایش تاثیر منفی محصولات کاهش کیفیت بر افزودنی های روغن نو را نشان داد.
گزینه هایی برای فلاش کردن سیستم های روغن توربین
زمانی که امکان به کارگیری تعداد متفاوتی از تکنیک های فلاش کردن روغن وجود دارد، می توان آن ها را به سه دسته تقسیم کرد: فلاش کردن شیمیایی، فلاش کردن مکانیکی و افزایش حلالیت سیستم پاک کننده[۱]
[۱] solubilityenhanced system cleaning
فلاش کردن شیمیایی
با این روش، یک سطح فعال از نظر شیمیایی، به منظور حذف وارنیش و لجن از سیستم استفاده می شود. عامل سطحی فعال پاک کننده، معمولاً یک محلول قابل حل در روغن، برپایه ترکیبات نفتنیک، همراه با شوینده ها، پخش کننده ها و بازدارنده های خوردگی است. عامل سطحی فعال، اغلب به روغن توربین در حال کار، ۴۸ ساعت قبل از خروج آن با سرعت ۱۰ درصد اضافه می شود. معمولاً جهت فیلتر شدن مقدار زیاد آلودگی آزاد شده در طی فلاش شدن، نیاز است فیلتراسیون تکمیلی انجام شود.
سپس روغن در حال کار و پاک کننده آن، از سیستم خارج می شوند و روغن فدا شونده[۱] جهت فلاش کردن، برای شستشوی باقیمانده پاک کننده از سیستم استفاده می شود. به تناوب، چند شارژ جزئی دیگر با روغن فلاش کننده، جهت رقیق سازی کافی پاک کننده سیستم، لازم است. گاهی، سیالات بر پایه آب همراه با پاک کننده به عنوان روغن فلاش کردن به کار گرفته می شود.
[۱] sacrificial flushing oil
فلاش کردن مکانیکی
در زمان فلاش کردن مکانیکی، روغن گرم شده توسط یک پمپ خارجی با سرعت از میان سیستم عبور داده می شود. سرعت جریان، معمولاً سه تا چهار برابر سرعت معمول جریان است و به حداقل، عدد رینولدز[۱] ۴۰۰۰ برای تبدیل به جریان آشفته[۲] نیاز است. به منظور محافظت از سطوح یاتاقان از آلودگی های ساینده، جامپرهای یاتاقان[۳] جهت افزایش کارایی یاتاقان نصب می شوند تا سرعت جریان به حالت مناسبی برگردد.
سایر قطعات مانند هدرهای سیستم[۴] و شیرها[۵] از فلاش کردن ایزوله می شوند. فیلتر های جریان جانبی مکمل[۶] (معمولاً فیلترهای کیسه ای[۷])، جهت جمع آوری آلودگی های رانده شده سیستم از جریان آشفته روغن توربین، نصب می شوند. تمیز کردن دستی قطعات، اغلب با فلاش کردن مکانیکی همراه است.
[۱] Reynolds number
[۲] turbulent flow
[۳] .Bearing jumpers
[۴] system headers
[۵] valve blocks
[۶] Supplemental sidestream filters
[۷] bag filters
افزایش حلالیت سیستم پاک کننده
در این روش از فلاش کردن، سه ماه قبل از زمان برنامه ریزی شده جهت قطع سیستم، به روغن توربین در حال کار، یک عامل افزاینده حلالیت سازگار، افزوده می شود. خواص شیمیایی این افزودنی، به میزان زیادی ویژگی های کنترل رسوبات روغن را بهبود می بخشد. نحوه عمل به این صورت است که با افزایش حلالیت سیال در حال کار، رسوباتی مانند لجن و وارنیش می توانند دوباره جذب روغن شوند.
درهنگام قطع سیستم، روغن در حال کار و عامل افزاینده حلالیت از سیستم خارج شده و مخزن تمیز شده با روغن نو، پر می شود. از آن جایی که افزاینده حلالیت با روغن در حال کار، سازگاری دارد، نیازی به شستشو با روغن فدا شونده نیست.
توانایی روغن در دوباره حل کردن رسوبات به داشتن انرژی آزاد منفی از لحاظ ترمودینامیکی بستگی دارد. اصل لوشاتلیه (قانون تعادل) توازن این انرژی را با حل کردن رسوبات بیشتر در روغن، کنترل می کند. اضافه کردن عامل افزاینده حلالیت به روانکار، حلالیت آن را افزایش داده و انرژی جنبشی مورد نیاز برای دوباره حل کردن رسوبات و برگرداندن آن به سیال را تامین می کند.
در بسیاری از موارد سه ماه قبل از خارج کردن روغن، سیستم فیلتراسیون شیمیایی اسلیپ استریم[۱]، به روغن توربین متصل می گردد. سیستم فیلتراسیون باید قابلیت حذف محصولات کاهش کیفیت حل شده از روغن را داشته باشد. در این صورت، امکان حذف آلودگی ها به طور مستمر از روغن فراهم شده و به سیال توانایی حل دوباره آلودگی ها را می دهد.
خدمات فلاش کردن روغن اغلب، ترکیبی از فناوری ها و تکنیک های فلاش کردن همراه با یکدیگر است. هرچند در تمام موارد لازم است تا فناوری های گوناگون با منابع و هدف فلاش کردن روغن شما تطبیق داده شود.
[۱] a slipstream chemical filtration
مطالعه موردی: فلاش کردن دو پمپ تغذیه دیگ بخار
نیروگاه برق زغال سنگ سوز[۱] با دو پمپ تغذیه دیگ بخار[۲] ۳۰۰۰ گالنی و روغن توربین قدیمی که تا اندازه زیادی کاهش کیفیت داده، مدنظر بوده است. دو نوع متفاوت از خدمات، جهت تمیزی سیستم در نظر گرفته شد.
برای اولین پمپ یک شرکت حرفه ای، فلاش کردن روغن در طی قطع برنامه ریزی شده سیستم را به عهده گرفت. در ابتدای قطع سیستم روانکاری خالی و آماده شد. نواحی با جریان محدود و قطعات بحرانی با ایجاد جامپر هوزهای تخصصی شده[۳]، از سایر سیستم جدا شدند. محفظه پاک کننده[۴] با فضای محدود بر مخزن[۵] سوار شد. محلول آبی با پاک کننده اسیدی به سیستم اضافه شد. پمپ خارجی و فیلترهای کیسه ای برای تولید سرعت جریان بالا استفاده شد.
[۱] a coalfired power plant
[۲] boiler feedwater pumps
[۳] specialized jumper hoses
[۴] tank cleaning
[۵] reservoir
در نتیجه فلاش کردن شیمیایی، آب از سیستم به وسیله تبخیر و زهکشی خارج شد. سیستم با روغن نو پر شد. فلاش با سرعت و دمای بالا برای حذف هر نوع آلودگی از سیستم اجرا شد.
کل زمان صرف شده برای فلاش با روغن، ۵/۲ هفته به طول انجامید. در حین قطع سیستم، حدود ۱۰۰ ساعت برای آن زمان صرف شد. هزینه تمام شده $ ۱۵۰۰۰۰ بود. فلاش روغن موفقیت آمیز بود و تمام وارنیش و آلودگی ها از سیستم حذف شدند.
برای پمپ دوم، روش افزایش حلالیت پاک کننده سیستم روی دستگاه اعمال شد. عامل افزاینده حلالیت، سه ماه قبل از قطع سیستم به آن افزوده شد. یک سیستم فیلتر کردن مناسب شیمیایی جهت تمیزسازی مستمر سیال نصب شده و توانمندی سیال جهت حل آلودگی ها را برگرداند. در حین قطع، روغن مصرفی از مخزن و تمام نقاط پایین سیستم زهکشی شد. سپس روغن نو به سیستم اضافه شد.
کل زمان صرف شده برای تمیز کردن سیستم، سه ماه به طول انجامید. طبق زمان تخمینی، ۸ ساعت برای انجام فلاش روغن صرف شد. قیمت تمام شده $ ۵۰۰۰۰ بود. در این مورد نیز تمام وارنیش و رسوبات، از سیستم حذف شده و فلاش روغن با موفقیت انجام شد.
میزان رضایت از دو روش فلاش دستگاه، مشابه بود. با این حال سیستم افزاینده حلالیت پاک کننده سیستم، یک سوم هزینه را در برداشته و کمتر به منابع داخلی جهت حمایت نیاز داشت. همچنینی نگرانی ها پیرامون پس ماندهای عوامل پاک کننده در روغن توربین، برطرف شد.
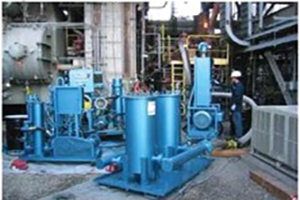
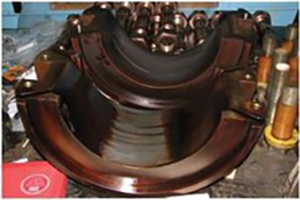
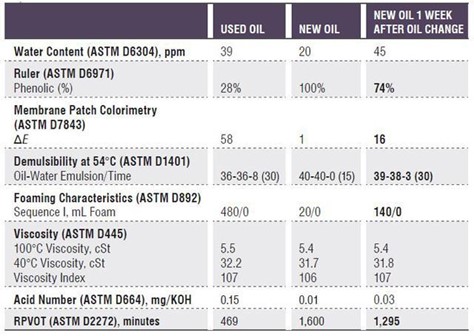
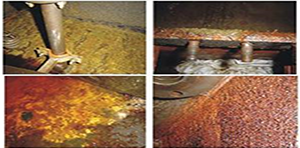
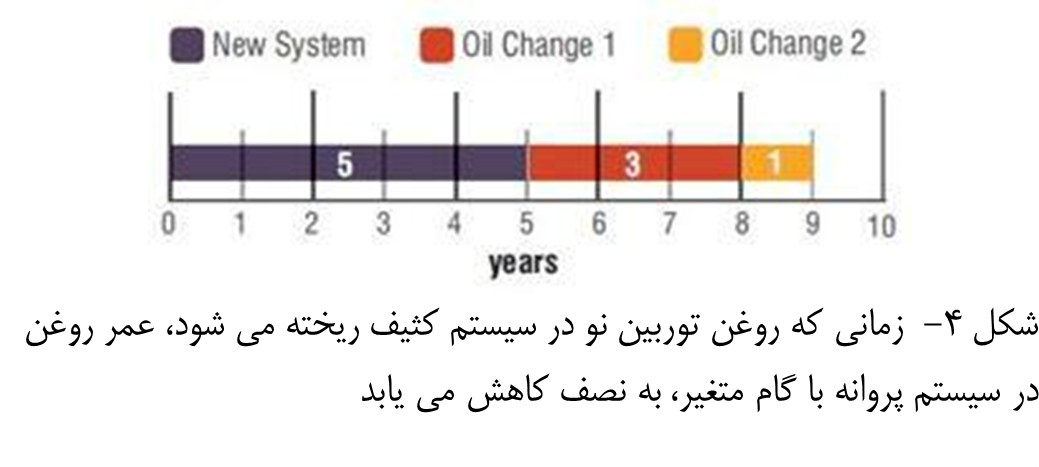
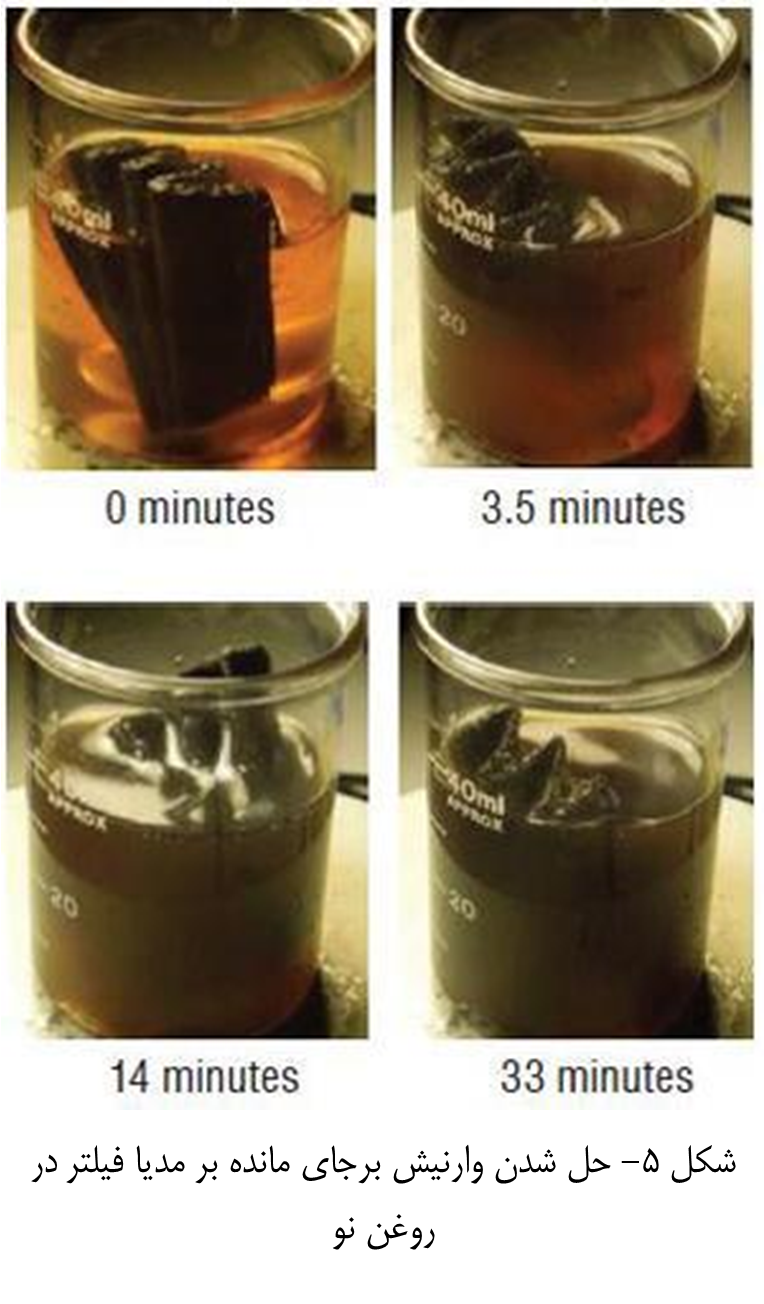
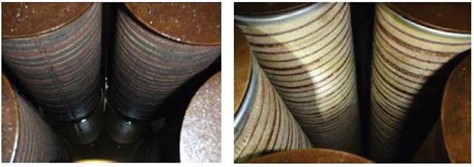
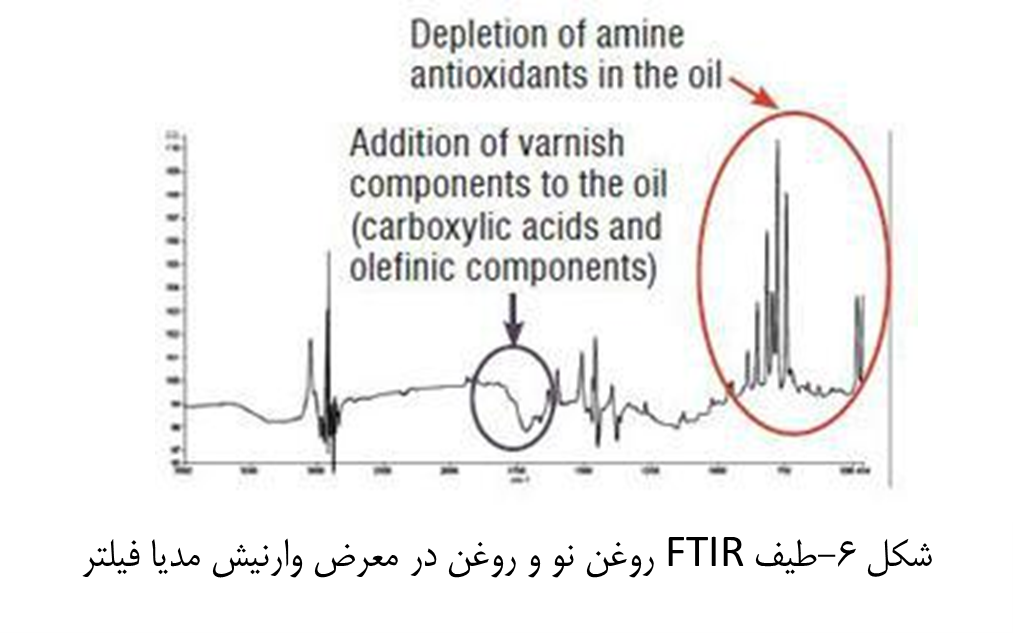